55 Dicas e práticas recomendadas para separação de pedidos de armazém especializado
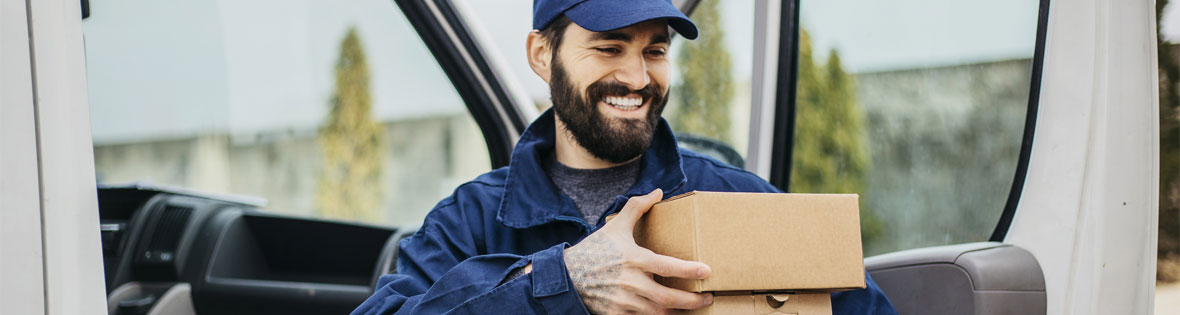
Existem muitos processos de entrada e saída envolvidos na movimentação e gerenciamento de estoque que constituem a disciplina de gerenciamento de armazém. As empresas geralmente se concentram em processos de saída para aumentar a satisfação do cliente e reduzir as ineficiências e custos operacionais.
Mas a separação de pedidos é uma parte crucial da parte de saída do gerenciamento de depósito. Constitui todas as etapas envolvidas na recuperação física dos itens armazenados no depósito para atender a um pedido do cliente.
Importância de melhorar a seleção de pedidos no armazém
Empresas inteligentes procuram melhorar a coleta de pedidos por um bom motivo - é a atividade mais trabalhosa e cara no depósito, normalmente responsável por mais da metade dos custos operacionais do armazém.
As melhorias na seleção de pedidos ajudam as empresas a fornecer os produtos certos aos clientes com mais rapidez, e gaste menos dinheiro nas etapas associadas. Os seletores de pedidos de armazém normalmente pegam uma lista de seleção e viajam para diferentes pontos no armazém para obter os itens, procure por eles nas prateleiras do armazém, extraí-los e combinar a papelada para garantir a precisão do pedido antes do envio.
A parte mais demorada do processo de separação de pedidos é viajar, que ocupa 55% do tempo do seletor de armazém, na média, seguido por papelada e outras atividades (20%), pesquisando (15%) e extraindo (10%), de acordo com pesquisa do Instituto de Logística e Cadeia de Suprimentos da Georgia Tech. Por esta razão, muito do trabalho para melhorar os processos de separação de pedidos visa reduzir o tempo improdutivo de viagens.
Alcançar a melhor seleção de pedidos da categoria exige saber onde estão os produtos, exatamente quantos estão disponíveis, sabendo quantos você precisa - para que você não escolha para cada pedido individual um de cada vez - e garantindo que eles estejam estrategicamente posicionados para facilitar a coleta e o processamento rápidos para envio.
Então, como as empresas podem minimizar o tempo de coleta de pedidos e, ao mesmo tempo, garantir o atendimento preciso dos pedidos e a segurança dos funcionários em um depósito?
55 Dicas e práticas recomendadas para a coleta de pedidos de armazém
Como não há uma maneira única de garantir pedidos perfeitos, existem muitos métodos, ferramentas e processos que uma empresa pode empregar para melhorar a seleção de pedidos. A combinação de estratégias, as melhores práticas e tecnologias que sua organização deve adotar dependerão da indústria, número de itens vendidos e velocidade com que o estoque se move pelo (s) depósito (s).
Observar o design do armazém e os métodos de separação de pedidos usados dentro de suas quatro paredes ajudará uma empresa a selecionar os processos adequados, tecnologias e equipamentos para melhorar a coleta de pedidos.
Dicas de design de armazém para a seleção de pedidos
A excelência na seleção de pedidos começa com a escolha do design e fluxo de depósito corretos para sua estratégia de processos de negócios.
-
Escolha um tipo de depósito e fluxo. Os depósitos geralmente são projetados para movimentar mercadorias em um dos layouts abaixo (ou alguma combinação deles).
- Fluxo em forma de U posiciona as docas de recebimento e despacho no mesmo lado do edifício, e os produtos se movem em forma de U do recebimento ao despacho. Este projeto oferece espaço de encaixe compartilhado e normalmente é melhor para edifícios pequenos.
- Fluxo em forma de I coloque o recebimento em uma extremidade e a expedição na outra extremidade do edifício, de forma que todas as mercadorias se movam em uma única direção. Um fluxo em forma de I é bom para empresas de alto volume, bem como aqueles que precisam de forte controle de segurança sobre as mercadorias que entram e saem do depósito.
- Fluxo de armazém em forma de L tem descarga de entrada em uma extremidade e remessa de saída em um ângulo perpendicular a essa área. Isso pode tornar o cross-docking - quando os itens são retirados de um caminhão e imediatamente carregados em outro - mais fácil. Isso é bom para empresas que nunca podem estocar produtos em prateleiras, enviando estoque logo após trazê-lo.
-
Decida como o produto é organizado dentro desse fluxo. Isso poderia ser o que é chamado de design de armazém triádico, que é dividido em três zonas - movimento rápido, produto de movimento médio e lento. Em armazéns que não usam este design, o produto não está zoneado. Muitos armazéns adotam um design no qual automatizam uma seção com itens adequados e ainda tendo pessoas envolvidas na coleta de itens, até certo ponto, no outro.
- Coloque os produtos de movimento mais rápido perto do preenchimento para que sejam fáceis de escolher.
- Armazene itens que costumam ser vendidos juntos, próximos uns dos outros.
Métodos de separação de pedidos de armazém
Se você não tem um método de separação, você irá separar para cada pedido cronologicamente sem visibilidade dos outros pedidos em sua fila - isso leva a muito tempo perdido no depósito para recuperar o mesmo item ao longo do dia.
-
Operações com baixo volume de pedidos ou que vendem produtos sofisticados ou pesados devem ser discretas, escolha de pedido individual, separação de peça ou selecionador de peça. Este é o método de coleta de pedidos mais simples, em que uma pessoa escolhe o pedido completo, andando pelo armazém, puxando todos os itens necessários e, muitas vezes, consolidando-os em um recipiente.
-
Para organizações que precisam selecionar e embalar pedidos de vários itens rapidamente e têm um grande número de SKUs e coletas por pedido, a captação de ondas é uma boa escolha. A coleta é realizada em ondas programadas, e todas as zonas são selecionadas ao mesmo tempo. Os itens são classificados a jusante à medida que são preparados para remessas individuais. Escolha locais como pedidos em conjunto com base em regras predefinidas e libere-os para serem atendidos juntos para que os selecionadores possam escolher para toda a onda ao mesmo tempo.
-
Para aumentar a eficiência da coleta, os trabalhadores podem retirar em lotes onde coletam para vários pedidos - como itens semelhantes ou localizados em áreas semelhantes - em uma viagem. Para empresas com um baixo número de escolhas por pedido, a separação em lote pode reduzir o tempo de viagem. O operador vai para o armazém, escolhe a quantidade total de itens necessários e, em seguida, os aloca para cada pedido individual.
-
Para grandes armazéns com muitos SKUs, a separação por zona costuma ser vantajosa. A coleta de lote pode incorporar o método de coleta de zona, em que um seletor é encarregado de cuidar de uma determinada área do armazém, obter todos os itens de sua zona e, em seguida, passar o pedido adiante. Por esta razão, a separação por zona também é conhecida como pegar e passar. Os itens podem se mover, por exemplo, ao longo de uma correia transportadora até que todos os itens necessários estejam na caixa.
-
Empresas inovadoras estão tentando configurações e sistemas de classificação adequados para aumentar a eficiência do processo de separação. O seletor de armazém permanece em um lugar, e os produtos são trazidos para o seletor por um transportador, um dispositivo robótico ou alguma outra tecnologia automatizada. Pense em pessoa para pessoa como a automatização do processo de separação discreta.
-
Outra forma de reduzir o tempo de viagem é pick-to-box. Pick-to-box integra mais automação em batch picking. As áreas de coleta podem ser organizadas em estações de coleta, cada um conectado por uma correia transportadora. O seletor enche a caixa com os produtos pelos quais é responsável e movimenta a caixa até que o pedido seja atendido.
Equipamento e tecnologia de coleta de pedidos de armazém
Outro aspecto importante do gerenciamento de warehouse é a tecnologia que dá suporte à estratégia ideal para as instalações e a natureza do negócio. Por exemplo, uma empresa com um baixo número de SKUs e menos linhas selecionadas pode empregar um método de seleção de pedido individual, e alavancar a tecnologia pick-to-belt ou pick from pallet. As empresas com um grande número de SKUs que movimentam grandes volumes podem optar por separação em lote e tecnologia de voz ou separação por luz.
Ao considerar quais equipamentos e tecnologias são adequados para o seu armazém:
-
Alinhe a tecnologia com o número de SKUs e o volume. Observe o número de linhas sendo processadas por dia em relação ao número de produtos. Em geral, quanto maior o número de SKUs e o número de linhas, quanto maior a necessidade de automação.
-
Comece implementando um sistema de gerenciamento de armazém (WMS). Mesmo as operações de warehouse mais simples precisam de alguma forma de sistema de gerenciamento de warehouse. Procure a funcionalidade básica de separação de pedidos para armazenar e rastrear SKUs e localização de itens e automatizar a criação de listas de separação de pedidos de clientes. Um WMS verificará o pedido do cliente em relação ao estoque disponível e fornecerá instruções na forma de uma lista de seleção. Leva em consideração o layout do armazém, a mão de obra disponível e a localização do equipamento para maximizar a eficiência e garantir a precisão na seleção de pedidos.
-
Integre alguma forma de tecnologia de separação móvel. Dos scanners de RF móveis básicos, para tecnologias que direcionam as escolhas iluminando botões nas prateleiras em um caminho de escolha (escolha para luz) ou guiam um seletor de fone de ouvido por voz (escolha para voz), existem muitas tecnologias móveis que são essenciais para a seleção precisa de pedidos, guiando os usuários para o corredor exato, prateleira, ou bin no caminho mais lógico. Certifique-se de que as tecnologias usadas no chão possam conversar facilmente com o WMS para que você não introduza complexidade desnecessária.
-
Certifique-se de que o WMS esteja integrado ao sistema ERP. O rastreamento de movimento e mercadorias no depósito fornece uma riqueza de dados valiosos para outros departamentos, como compras ou atendimento ao cliente. Certifique-se de que essas outras funções tenham acesso aos mesmos dados dentro do software que usam para seus trabalhos.
-
Selecione o sistema de manuseio de materiais correto e ajuste os sistemas conforme SKUs e aumento de volume. Um aumento no número de SKUs requer muito mais logística no armazém. Com SKUs baixos e baixo volume, um sistema simples de manuseio de materiais como empilhadeiras pode fazer, mas conforme o volume e a complexidade aumentam, o negócio precisará de mais mecanização. O equipamento de manuseio de materiais é um espaço inovador que alavanca muitas ideias e tecnologias inovadoras.
-
Considere os avanços nos equipamentos para permitir a configuração do corredor estreito. Otimizar o espaço disponível no depósito oferece vantagens além do armazenamento - também pode ajudar a reduzir o tempo de viagem no processo de coleta de pedidos. Os corredores convencionais do armazém têm de 12 a 14 pés de largura. Corredores estreitos têm normalmente 8-10 pés, mas pode ter pelo menos um metro e oitenta. Combinando as tecnologias e equipamentos certos, os armazéns podem obter ganhos na separação de pedidos com corredores mais estreitos.
-
Maximize o espaço do armazém usando o equipamento certo. A tecnologia de empilhadeiras está melhorando constantemente, e há caminhões capazes de passar por corredores estreitos e em espaços apertados, como a empilhadeira articulada. A Amazon aproveita robôs que se parecem com aspiradores Roomba. Esses robôs transportam os itens necessários das prateleiras para o selecionador e os empurram de volta para lugares apertados quando todos os itens são recuperados.
-
Implementar tecnologia de transporte. Existem dezenas de tipos de tecnologia de transporte que podem ser usados para uma coleta mais eficiente, bem como a saúde ergonômica dos funcionários que realizam o trabalho.
-
Veja os avanços nas tecnologias de classificação. Combinado com transportadores, tecnologias de classificação fornecem um aumento de precisão e eficiência - produzindo prazos de entrega mais curtos e mais precisão.
-
Descubra qual armazenamento é certo para a empresa e não negligencie os benefícios das tecnologias automatizadas. Um carrossel, por exemplo, automatiza a separação por meio de uma estante que gira ao longo de uma trilha para trazer os itens para o selecionador. Eles podem ser configurados para o método de separação escolhido pela empresa.
-
Compreenda todas as opções de tecnologia de separação automatizada disponíveis. Algumas empresas têm muito sucesso com equipamentos pick-to-light ou pick-to-voice. Com pick-to-light, os selecionadores leem o código de barras de um pedido e a quantidade e localização do item acendem. Pick-to-voice orienta o selecionador e fornece confirmação por meio de um fone de ouvido. Hoje, tecnologias de realidade aumentada estão permitindo avanços, como óculos pick-via-smart, que exibem a localização e quantidade de um item digitalmente por meio de um fone de ouvido vestível. Eles fornecem instruções guiadas por voz e a capacidade de escanear diretamente com o fone de ouvido - liberando o trabalhador para usar as duas mãos e maximizar a eficiência com menos toques.
-
Implementar tecnologias inteligentes. As tecnologias IoT podem ajudar a fornecer contagens de inventário em tempo real, enquanto o avanço da tecnologia de wearables, como óculos inteligentes, torna mais fácil acompanhar o movimento do estoque e garantir que a contagem correta esteja lá para começar. Isso economiza o tempo do seletor e a frustração de procurar itens que não estão lá.
-
Explore o potencial dos robôs selecionadores. Os robôs selecionadores podem realmente fazer a coleta, com a capacidade de alcançar prateleiras altas e buscar itens para embalar, enquanto também equipado com sensores que os impedem de esbarrar em pessoas ou prateleiras.
-
Conheça co-bots. Co-bots podem ser úteis para implantar tarefas que têm alguma repetição, mas também requerem algum nível de intervenção humana. O co-bot pode montar a caixa, por exemplo, ou recupere itens com formato ou peso previsíveis - como uma caixa de sapatos.
Melhores práticas e estratégias de coleta de pedidos de armazém
O projeto do armazém, os métodos e tecnologias de coleta de pedidos ajudarão a determinar quais das estratégias abaixo fazem mais sentido implementar para melhorar seus processos de coleta de pedidos.
Comece com um objetivo claro sobre o que você deseja melhorar e como irá medi-lo, em seguida, selecione as dicas que fazem mais sentido.
-
Pergunte às pessoas que trabalham no warehouse onde estão os gargalos. Não se esqueça das muitas pessoas que costumam apoiar seus processos, incluindo administradores de escritório, operadores de equipamentos e outros.
-
Não baseie as metas de seleção de pedidos em médias. A sazonalidade e as tendências econômicas afetarão muito a forma como o estoque entra e sai do depósito. Olhe para os picos e depressões, aplique estatísticas e use algoritmos para determinar objetivos razoáveis.
-
Rastreie a produtividade do seletor. Conhecer os níveis de produtividade permite que o gerente de depósito projete turnos de acordo com a melhor divisão do trabalho. Veja as escolhas médias por pessoa-hora, bem como o inverso, pessoa-hora média por escolha. O trabalho médio por pedido é, então, o número médio de linhas de coleta por pedido vezes a média de horas por pessoa por coleta.
-
Meça e melhore o tempo total do ciclo do pedido ou o tempo do ciclo interno do pedido. A separação de pedidos é uma grande parte do cálculo do tempo total necessário para processar um pedido. O rastreamento desse número fornece uma medida da eficiência da separação.
-
Observe a precisão da contagem de estoque por localização e selecione as falhas de localização (como falta de estoque / pedidos em espera). Isso indica que não há uma quantidade suficiente no local designado.
-
Meça a taxa de atendimento (por linha e pedidos) para comparar os itens enviados naquele dia com o total de itens pedidos naquele dia. A taxa de preenchimento é uma boa maneira de garantir que as operações do armazém atendam à demanda do cliente e normalmente é calculada diariamente.
-
Meça a precisão da seleção de pedidos. A precisão da seleção de pedidos é o número três nos benchmarks mais importantes para armazéns no relatório de benchmarking DC Measures de 2020. Uma baixa precisão na seleção de pedidos aponta para a necessidade de processos mais eficientes, melhores padrões de controle, treinamento mais aprofundado e muito mais.
-
Não se esqueça dos KPIs que medem a produtividade dos funcionários. Isso inclui linhas despachadas escolhidas por hora, linhas despachadas por horas diretas, linhas despachadas por centro de distribuição total (CD) horas, Horas DC totais anuais / custo DC total e custo DC por mão de obra total usada.
-
Selecione no máximo seis benchmarks, métricas de segmentação que ajudarão a gerenciar o warehouse de forma mais eficiente e comparar a eficiência de várias instalações.
-
Reveja o espaço do seu armazém sempre que fizer a contagem física. Um depósito de bens de consumo em rápida movimentação precisará ser atualizado pelo menos a cada cinco anos, à medida que mudam as gamas de produtos, os apetites dos consumidores e as forças econômicas maiores. Deixar de evoluir o design do armazém impedirá as estratégias e melhorias de separação de pedidos.
-
Pratique a contagem cíclica para eliminar a complexidade e o desperdício de SKU.
-
Técnicas como a análise de estoque ABC (da qual existem diferentes tipos) permitem que as empresas classifiquem e organizem SKUs e removam ou movam produtos que estão obstruindo suas operações.
-
Vá além da classificação de SKUs apenas por volume de dólares, mas também como cada SKU consome recursos como mão de obra e espaço. Classifique os SKUs pelo número de vezes em que foram escolhidos durante um determinado intervalo, lucratividade, ou dificuldade de fabricação, por exemplo.
-
Implemente alguns princípios enxutos. Realize caminhadas regulares no Gemba - gastando tempo observando os processos do warehouse e realmente entendendo como eles são concluídos - para identificar ineficiências na instalação. As empresas também podem implementar técnicas de poka-yolk, onde eles testam suas operações à prova de erros e procuram maneiras de evitar erros inadvertidos. Um exemplo aqui é ver como o cross-docking pode melhorar o fluxo no warehouse.
Dicas de coleta de pedidos de armazém
Assim que a equipe do depósito souber onde a empresa concentrará seus esforços, ele pode começar a implementar as dicas abaixo para aumentar a eficiência e a precisão e melhorar a segurança do trabalhador.
-
Armazene SKUs populares juntos. A densidade da seleção pode ser aumentada, pelo menos localmente, armazenando os SKUs mais populares juntos. Então, os selecionadores de pedidos podem fazer mais escolhas em uma pequena área, reduzindo a quantidade de espaço que precisam cobrir e aumentando a produtividade.
-
Preste muita atenção ao entalhe do produto. Slotting refere-se à colocação cuidadosa de caixas individuais dentro do armazém, de forma que tipos semelhantes de inventário sejam armazenados juntos. Eles podem ser agrupados por tamanho físico, itens frequentemente pedidos juntos, sazonalidade e muito mais. Ao encaixar corretamente o produto, as organizações podem alcançar até 30% de economia de mão de obra e também garantir melhor ergonomia no depósito, Diz o Segredos da Cadeia de Abastecimento. Slot de acordo com o volume e movimento e revisitar a estratégia uma ou duas vezes por ano. Um WMS pode ajudar a identificar estratégias de alocação adequadas e há muitos algoritmos que podem ajudar aqui.
-
Lote os pedidos de uma única linha. Pedidos de linha única são pedidos de clientes para apenas um item. Por esta razão, eles não exigirão classificação no final de um caminho de separação e você pode ganhar eficiência fazendo com que um selecionador obtenha o máximo possível em uma viagem.
-
Equilibre o reabastecimento e a coleta para garantir que os itens estejam lá. O Segredos da Cadeia de Abastecimento diz que uma regra prática é um reabastecedor para cada cinco selecionadores, mas que depende dos padrões particulares de fluxo. As vezes, os armazéns cometem o erro de apenas medir os produtos pela receita de vendas, quando devem observar o movimento do produto, levando em consideração o volume e as vendas.
-
Certifique-se de que a papelada certa esteja associada ao pedido certo. Um quinto do tempo de um seletor de armazém é gasto para garantir que a papelada esteja correta, por Georgia Tech. Isso pode ser muito facilitado com a implementação de scanners de RF, que automatizam o processo, bem como garantem a precisão, imprimindo a guia de remessa do pedido.
-
Estruture listas de seleção para embalagem eficiente. Pense em como os itens vão caber melhor na caixa em que serão enviados. Um WMS pode sequenciar as coletas em uma lista de seleção para que os itens grandes sejam coletados primeiro, por exemplo.
-
Maximize a densidade de acertos. Uma maneira de fazer isso é aumentar a densidade das escolhas, minimizando a distância entre separações para aumentar o número de separações por ponto e, por sua vez, aumentar a produtividade.
-
Não misture SKUs múltiplos nos mesmos locais de armazenamento. Muitos depósitos ainda têm um local de armazenamento que está vinculado apenas a um nível de prateleira contendo até dez SKUs diferentes. Isso exige que o funcionário procure em vários produtos o item correto.
-
Tente minimizar o toque das mercadorias. Na maioria dos armazéns, sete a oito pessoas da entrada e saída para a gestão do armazém tocam em um item, mas as melhores empresas terão apenas três a quatro toques. Uma maneira de minimizar os toques é os seletores escolherem os itens e colocá-los diretamente na caixa de envio, não caixas de plástico em um carrinho.
-
Integre medições de peso com WMS. As empresas que enviam itens grandes e pesados podem aumentar a precisão da seleção de pedidos, vinculando as informações sobre o peso do item à lista de seleção. Se a escolha for, por exemplo, uma unidade curta, o sistema notificará automaticamente o trabalhador de que o peso está muito baixo e o instruirá a adicionar mais uma unidade.
-
Escolha da pilha de chão. Uma estratégia de alocação de produto é permitir que os selecionadores selecionem itens de alta rotação de caixas em paletes no chão, usando um porta-paletes ou porta-paletes. Isso pode ser mais eficiente do que manter esses itens de venda rápida em estantes de paletes altas.
-
As pessoas deveriam escolher usando carrosséis horizontais em vez de elevadores verticais. Vários esforços de benchmarking ao longo dos anos demonstraram que custa mais escolher verticalmente do que horizontalmente. Mas a utilização da capacidade do armazém exige que as coisas também sejam armazenadas verticalmente. Escolha os itens de velocidade mais lenta do armazenamento vertical e mantenha os itens de alta velocidade no nível do chão.
-
Escolha em uma área de seleção rápida ou de avanço. As empresas estão projetando áreas de seu depósito para abrigar SKUs populares que ficam no nível do solo e são reabastecidos por estoque de outras áreas do CD. Georgia Tech diz que a área de separação direta mais comum é a estante de paletes no piso térreo, que é reabastecida pela movimentação de paletes de níveis superiores. Outros exemplos são um rack de fluxo de caixa reabastecido do armazenamento a granel, ou equipamento especializado como um carrossel ou A-frame que é abastecido em outro lugar.
Tomar medidas para treinar e cuidar das pessoas que trabalham no depósito é outra parte crítica para garantir a eficiência, separação de pedidos precisa e econômica.
-
Certifique-se de que o raciocínio por trás da estratégia de gerenciamento de armazém e por que é importante para o negócio seja compreendido por todos os funcionários do armazém, não apenas gerentes. Um ótimo exemplo de por que isso é importante vem da SI Systems, que aponta que, quando muitas empresas implementam a verificação de código de barras duplo, onde o operador verifica o SKU do produto e, em seguida, o palete, para melhorar a precisão. Contudo, o operador frequentemente faz a varredura dupla do palete, porque é mais rápido. O funcionário faz isso porque deseja atingir os níveis de produtividade ou rendimento e não percebe por que a digitalização de ambos é crucial para a precisão do inventário. Você deve conduzir um processo de treinamento formal com os membros da equipe e explicar a justificativa de negócios para cada parte de um processo.
-
Use métricas reais para definir padrões de desempenho realistas para funcionários de warehouse. Use métricas como linhas de pedido escolhidas por hora e custo de separação para cada linha de pedido e procure melhorá-los, dando aos selecionadores as tecnologias certas que irão facilitar o aumento da eficiência e precisão, como pick-to-light e pick-to-voice.
-
Promova a cooperação. Um painel de controle de qualidade ou centro de controle pode ajudar a monitorar o desempenho geral do armazém para recompensar e encorajar as equipes, mas procure também destacar os ganhos individuais dos funcionários. Exiba estatísticas de alto desempenho e incentive o desempenho de alta produtividade e segurança.
-
Trabalhe para reduzir as horas extras. Compare as horas gerais com a produção e observe as linhas de pedidos escolhidas por hora de trabalho, por exemplo, para medir a eficiência do trabalho. Fator em horas normais trabalhadas versus horas extras, linhas escolhidas por dia e número de caixas, eaches ou paletes separados por período. Compare este período ao longo do período. Se esses números forem baixos, mas as horas extras são altas, descubra o porquê.
-
Tome medidas para tornar o local de trabalho mais seguro e em conformidade com os padrões da OSHA. As melhores operações de depósito têm programas formais de treinamento de segurança e treinamento contínuo. Coloque os produtos na chamada “zona dourada” para garantir uma saúde ergonômica adequada. Marque claramente os corredores e áreas de trabalho com marcadores de segurança e mantenha-os livres de detritos e perigos. Certifique-se de que todos os EPIs adequados sejam usados pelos trabalhadores do depósito em todos os momentos, incluindo capacetes, óculos, luvas, máscaras, uniformes adequados e muito mais.
-
Revise e refine os processos regularmente. Conforme as estratégias de produto mudam, certifique-se de que a estratégia de warehouse também funcione. Os desafios da cadeia de suprimentos e os esforços para aumentar a resiliência da cadeia de suprimentos desafiarão muitos dos princípios do gerenciamento de estoque just-in-time que guiaram as operações de armazenamento por anos. Em muitos casos, mais espaço será necessário e o estoque poderá ser mantido por longos períodos de tempo para ficar pronto para surtos e escassez. De fato, a demanda por espaço de depósito é alta - The Wall Street Journal relatou que a atividade imobiliária industrial aumentou 43% de abril a maio de 2020, com demanda por armazéns de mais de 100, 000 pés quadrados sendo o mais forte.
Otimize a seleção de pedidos com software de gerenciamento de armazém
Pense no pedido do cliente como uma lista de compras para o selecionador preencher, com cada entrada na lista (conhecidas como linhas de pedido) anotando o item e a quantidade. Idealmente, um sistema de gerenciamento de armazém está em vigor para verificar o estoque disponível e onde encontrá-lo, além de reorganizar os pedidos em uma lista de seleção que leva em consideração o layout do depósito para aumentar a velocidade. O número de linhas de separação pode ser uma indicação de quanto o trabalhador terá que viajar pelo depósito para obter os itens necessários para os pedidos.
As empresas podem recorrer aos sistemas de gerenciamento de armazém (WMS) para ajudar a gerenciar os processos de entrada e saída de seus armazéns e obter visibilidade de todos os SKUs estocados e de sua localização. A funcionalidade WMS se baseia em uma solução de gerenciamento de estoque, e também tem recursos para ajudar na estratégia de armazenamento e gerenciamento de força de trabalho. O WMS fornece detalhes sobre todos os itens no armazém - dimensões físicas, como está embalado, onde está armazenado e o caminho mais eficiente para chegar até eles.
Um WMS suporta o agendamento de consultas, recebendo, Garantia da Qualidade, por para fora, rastreamento de localização, gerenciamento de ordens de trabalho, escolhendo, embalagem e consolidação e envio. O WMS transforma o pedido do cliente em uma lista de seleção e rastreia a montagem do pedido. O WMS também pode gerenciar processos de entrada em um armazém, mostrando onde o estoque deve ser armazenado, rastreando a produtividade do trabalhador, garantindo que os pedidos atendam aos cronogramas de envio e muito mais. Ele também pode se conectar aos sistemas de gerenciamento de pedidos e ERP. Especificamente, para a função de separação, um WMS robusto pode suportar pick-to-light, Operações direcionadas por RF, planejamento de trabalho, Slot de SKU e muito mais.
O WMS certo será dimensionado conforme a nova funcionalidade é necessária e se adaptará conforme os processos mudam. Embora o próprio edifício possa permanecer estático, os processos e tecnologias de uma empresa não devem ser gravados em pedra. Olhando constantemente para os sistemas e como as pessoas os usam para realizar seu trabalho, a gestão do armazém pode ser constantemente melhorada, ajudando os funcionários a fazerem seu trabalho com mais eficácia e garantindo que os clientes continuem comprando e confiando em sua empresa.
O negócio
- 11 melhores planos de aposentadoria:prós e contras
- Quando comprar um estoque e quando vender um estoque:5 dicas
- Previsão de estoque:tipos,
- Inventário físico:etapas,
- 35 Métricas de comércio eletrônico com fórmulas, Benchmarks e dicas
- 51 dicas de gerenciamento de armazém para o seu negócio
- Guia definitivo para a seleção de pedidos:tipos, Métodos e dicas
- As melhores dicas, Truques, e ferramentas para trabalhar remotamente
-
Melhores dicas e informações úteis sobre como negociar criptomoedas
Antes de mergulhar de cabeça no comércio de Bitcoins, existem inúmeras dicas essenciais de que você precisa se antecipar uma jornada quase tranquila em seu novo empreendimento. Esta não é uma promessa...
-
É arriscado negociar Altcoins? - Melhores práticas e informações úteis
Em grande medida, esta pandemia atual devastou muitas empresas e setores financeiros, incluindo o mercado de criptomoedas. Embora o Bitcoin tenha dominado o mercado de criptomoedas e registrado um rec...