Alocação de armazém:o que é e dicas para melhorar
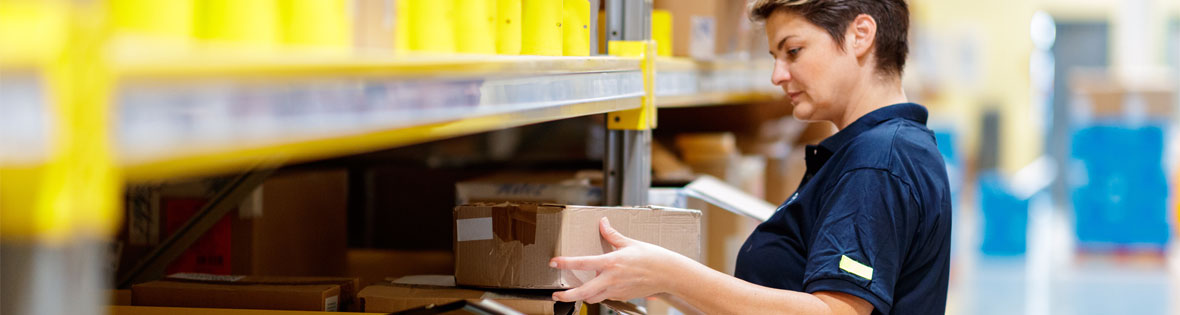
Os gerentes de instalações devem lidar constantemente com a complexidade crescente. Seus depósitos estão lidando com mais SKUs, e eles estão sob pressão para tirá-los de casa mais rápido. Com alocação de armazém, os gerentes das instalações podem reduzir custos e melhorar o desempenho. Eles podem fazer isso sem aumentar a pegada de seu prédio ou expandir a equipe.
O que é alocação de armazém?
Três unidades básicas se combinam para formar o armazém:itens, paletes e slots.
Os itens são do navio dos armazéns de mercadorias. Um slot é uma prateleira - ou parte de uma prateleira - onde esses itens ficam. Uma palete é uma estrutura projetada para ser levantada por uma empilhadeira. Os trabalhadores retiram os itens dos slots e os embalam em paletes. Eles são carregados em caminhões por meio de uma empilhadeira e levados embora.
A divisão do armazém envolve os planejadores que determinam o slot mais eficiente para os itens. Por exemplo, um gerente de instalação pode colocar um item de venda mais rápida em um slot mais próximo da doca de carregamento. Dessa maneira, ele carrega mais rápido.
A distribuição de alocação no armazém é complicada porque cada item possui um conjunto distinto de características. As complicações também ocorrem porque alocar itens significa lidar com prioridades sobrepostas. A velocidade pode ser uma consideração, mas a segurança também. Se uma empresa colocar todos os seus itens de venda mais rápida perto da doca de carregamento, o resultado pode ser paletes pesadas na parte superior ou desequilibradas. Isso pode colocar os trabalhadores em risco e contribuir para danos aos itens.
Dominar a alocação de depósitos significa pesar atributos e prioridades complexas. Um bom resultado tem muitos benefícios - aumentos na velocidade, segurança, satisfação do cliente e muito mais. Como as empresas podem fazer melhorias?
Principais vantagens
- Armazéns são bem-sucedidos ou falham com base em sua capacidade de melhorar a velocidade e reduzir custos
- Os processos de slot são mais do que uma maneira de enviar itens de alta velocidade rapidamente
- A alocação de depósitos tem o potencial de melhorar o desempenho dos lucros e da receita em toda a organização.
Alocação de armazém explicada
A alocação de depósitos representa uma oportunidade para os gerentes porque é difícil acertar. Muitos armazéns não se preocupam com o entalhe do armazém. Equilibrar as prioridades é complicado - há uma tentação, por exemplo, para simplesmente colocar todos os itens de movimento rápido em slots perto da doca de carregamento e viver com as consequências.
Quando os gerentes de armazém equilibram suas prioridades, eles podem aproveitar os benefícios do aumento da velocidade e, ao mesmo tempo, atenuar as desvantagens. Enquanto isso, se os gerentes só tentarem maximizar um único atributo, eles podem acabar diminuindo a segurança geral ou criando problemas - como engarrafamentos - que são contraproducentes para os fins que estão tentando alcançar.
A criação de um programa de alocação líder do setor envolve gerentes dispostos a iterar rapidamente, coletar dados e ouvir o feedback dos trabalhadores. O resultado é uma instalação que não opera apenas no pico da eficiência, mas ajuda a empresa a superar seus concorrentes.
Por que o alocação de estoque é importante
A alocação de depósitos é a pedra angular de um depósito otimizado. Quando feito corretamente, há resultados positivos nas linhas superior e inferior. O rendimento mais rápido cria eficiências operacionais e manuseio aprimorado, resultando em clientes mais satisfeitos - levando a redução da rotatividade e aumento da receita. Aqui estão alguns outros benefícios:
- Manuseio de item aprimorado
Uma consideração crítica em um ambiente de warehouse é que os itens não sejam danificados durante o transporte ou armazenamento. Uma boa distribuição de estoque significa que os itens são armazenados corretamente - alimentos perecíveis são armazenados em contêineres refrigerados, por exemplo. Isso significa que os clientes recebem seus itens em boas condições. - Armazenamento otimizado
Custa dinheiro armazenar itens em um ambiente de depósito. Os itens encaixados de forma eficiente ocupam menos espaço, o que significa que você pode armazenar mais itens na mesma área. - Cumprimento perfeito
A alocação do armazém torna mais fácil para os funcionários escolher e embalar os itens. Por exemplo, você pode reduzir os “engarrafamentos” garantindo que os trabalhadores que coletam itens menores raramente tenham que esperar enquanto alguém coleta os paletes usando uma empilhadeira. - Maior segurança
Com alocação de armazém, os gerentes das instalações podem criar uma ordem de separação otimizada que coloca os itens mais pesados na parte inferior de um palete e os itens mais leves no topo. Isso cria um palete mais seguro - um que não é desequilibrado ou pesado na parte superior - enquanto minimiza o risco de danos ao produto em trânsito.
Evite subestimar a importância de alocação de warehouse. Ao completar um processo de alocação eficaz, gerentes de instalações podem melhorar quase todos os aspectos de suas operações, estendendo-se além do departamento e no negócio em geral. Criar um processo de alocação significa aprender uma nova terminologia e fazer algumas escolhas difíceis, Contudo.
Alocação aleatória vs. alocação fixa:Qual é a diferença
Uma das primeiras escolhas que os gerentes de instalações fazem é entre alocação aleatória ou fixa.
Slotagem fixa
Ranhura fixa significa que cada item no depósito tem um local de depósito permanente. A classificação de cada caixa é para uma quantidade mínima e máxima de seu item atribuído. Se a lixeira ficar muito vazia, ele aciona um pedido de reabastecimento do armazenamento de reserva.
Alocação aleatória
A alocação aleatória significa que os itens são atribuídos a zonas de escolha em vez de locais de escolha permanentes. Se o estoque em um slot se esgotar, então, os selecionadores são designados para escolher esses itens de outro local dentro dessa zona. Quaisquer recibos recebidos são transferidos diretamente para as zonas de seleção, com pouco ou nenhum estoque de reserva mantido à mão.
Por que escolher um método em vez do outro? A ranhura fixa é tradicional em relação à forma como a indústria de armazém opera, mas pode estar se tornando menos relevante. Reabastecer os slots de itens do armazenamento de reserva pode ser um processo demorado, e os volumes crescentes de remessa exigem velocidades aumentadas. A alocação aleatória pode ser mais rápida porque há muito menos tempo gasto na reposição, mas as zonas de seleção podem ser muito maiores do que os locais de armazenamento permanentes. Resumidamente, alocação aleatória pode exigir um armazém maior.
Macro Slotting vs. Micro Slotting:Qual é a diferença?
No nível acima de alocação aleatória vs. alocação fixa, os gerentes de instalações também devem lutar contra macro slotting versus micro slotting.
Alocação de macro
Ao alocar macro, o gerente da instalação deve considerar o arranjo de suas zonas de seleção. Em um clima onde os clientes exigem frete em dois dias, esse layout é crítico - os armazéns devem apresentar projetos de alto rendimento com pouco congestionamento nas áreas de recebimento ou carregamento.
Micro slotting
Micro-slotting diz respeito à disposição de itens e paletes nas zonas de separação. Por exemplo, como os itens devem ser armazenados em uma prateleira individual? Micro slotting pode afetar significativamente o ecossistema do warehouse, principalmente relacionados à saúde e segurança do trabalhador. Por exemplo, colocar itens mais pesados nas prateleiras mais baixas pode forçar os trabalhadores a se curvarem para pegá-los - expondo-os a lesões por esforço repetitivo.
Não há um componente "versus" em relação a micro-alocação e macro-alocação. Os gerentes de instalações devem levar ambos os reinos em consideração enquanto organizam seu warehouse. Assim que as empresas tiverem alocação micro e macro sob controle, eles podem ver melhorias significativas em como seus armazéns operam.
Benefícios de alocação de armazém
Quando os gerentes das instalações começam o processo de alocação do armazém, eles freqüentemente precisam justificá-lo. Quais são os benefícios que o entalhamento de armazém produz? Os benefícios abaixo resultam de um processo de alocação bem gerenciado e podem ajudar a obter a adesão dos executivos para estabelecer esses processos dentro de sua organização.
Libere espaço
Tanto os depósitos com alocação aleatória quanto com alocação fixa precisam minimizar o estoque no armazenamento de longo prazo e, ao mesmo tempo, maximizar o estoque que pode ser imediatamente retirado e enviado. Um processo de alocação eficiente significa que mais espaço pode ser alocado para as áreas mais críticas do depósito.
Coleta mais rápida
A coleta mais rápida significa que é mais fácil para os selecionadores encontrar itens nos slots. Os trabalhadores sempre sabem a localização dos itens e como chegar lá, sem nunca procurar nas prateleiras.
Menos erros
Ocorrem erros se um item for perdido, danificados ou mal entregues durante o processo de separação. Garantir que o warehouse esteja organizado e com alocação correta minimiza esses erros, resultando em custos mais baixos e clientes mais satisfeitos.
Maior capacidade de armazenamento
O espaço é escasso nos armazéns. Os volumes de envio aumentam, mas os armazéns não podem expandir sem dificuldade. Um processo de alocação aprimorado ajuda a maximizar o espaço disponível, permitindo que as empresas coloquem mais itens na mesma área.
Reduza o tempo de viagem
Reduzir o tempo de viagem é um benefício que contribui para, mas distinto de, colheita mais rápida. Um trabalhador pode saber como chegar a um item, mas esse conhecimento não ajuda se seu caminho for ineficiente. As ineficiências são evidentes quando os trabalhadores precisam voltar muito para o armazém para pegar um item de movimento rápido ou separar os itens rapidamente em lados opostos de um único corredor. O slot de warehouse aprimorado elimina essas ineficiências, resultando em uma coleta e reabastecimento mais rápidos.
Aumente a visibilidade
O tempo que os funcionários passam olhando para a prancheta ou tablet para encontrar um item é quando eles podem pegá-lo e entregá-lo. Uma boa alocação ajuda a melhorar a produtividade dos funcionários, permitindo-lhes localizar itens imediatamente. Este processo ajuda os gerentes de instalações e funcionários a entender imediatamente quando um item é não no lugar certo, o que reduz a possibilidade de erros.
Minimize os danos do item
Além de evitar danos durante o transporte ou embalagem, uma estratégia de alocação de depósito também pode ajudar a evitar danos aos itens armazenados. Por exemplo, ajuda a garantir que os trabalhadores armazenem alimentos perecíveis apenas nas seções refrigeradas das instalações.
Custos de transporte reduzidos
O estoque não fica apenas parado - ele acumula custos de armazenamento quantificáveis a cada segundo que não envia para o cliente. Os processos de estoque just-in-time enfatizam a importância de manter muito pouco estoque disponível para reduzir os custos de manutenção do estoque. A alocação de depósitos ajuda a diminuir esses custos, aumentando o rendimento. Quanto mais rápido as empresas puderem gerenciar o estoque, menos tempo - e dinheiro - eles precisam gastar armazenando-o.
Dados necessários para configurar o alocação de armazém
Existem benefícios claros em criar uma estratégia de alocação de armazém concreta, Mas por onde você começa? Usando os dados da cadeia de suprimentos abaixo, os gerentes podem começar a criar um processo de alocação que otimize suas instalações.
Histórico de pedidos
Essas informações informam quais itens agrupar para melhorar a eficiência e as mudanças anuais ou sazonais no volume de pedidos.
Dados SKU
Os dados revelam que tipo de produto um item representa e suas dimensões. Isso ajuda os gerentes a entender quaisquer considerações especiais para armazenar ou manusear um item.
Nível de coleta de itens
Esta informação diz respeito se a separação ocorre no palete, caso ou nível individual. Ele também mostra o meio de armazenamento do qual o item é retirado.
Melhores práticas de alocação de armazém
Como os gerentes de instalações usam as informações acima para gerar uma estratégia de alocação?
Nível de item e meio de armazenamento
Uma estratégia de alocação deve considerar se eles selecionam um item no nível do palete, o nível do caso, ou uma única peça. Mover um palete ou caixa pode exigir uma empilhadeira ou um carrinho. Esses movimentos significam que outros trabalhadores da área devem contornar um obstáculo temporário, reduzindo sua velocidade. Uma boa estratégia garante o agrupamento de itens de alto nível em áreas onde eles não obstruam outros selecionadores.
Tamanho e peso do cubo
Os dados de SKU normalmente incluem informações como o tamanho e o peso de um item. É melhor garantir que um item pesado seja o primeiro na ordem de coleta, o que significa que os dados SKU são críticos. Também, os trabalhadores precisam montar cubos que não excedam as dimensões do palete embaixo. Portanto, os gerentes precisam priorizar como os itens de formato regular contribuem para a eficiência da embalagem.
Velocidade SKU / velocidade dos itens
O histórico de pedidos pode ajudá-lo a entender quais itens se movem mais rapidamente. Ele mostra quais itens entram e saem da instalação no menor tempo possível - e quais se movem mais lentamente. O agrupamento de itens de movimento rápido e lento pode ajudar a aumentar a velocidade de separação.
Itens de movimento rápido vs. itens de movimento lento
Os itens que se movem rapidamente são como parecem - eles entram no depósito e saem com a mesma rapidez. Geralmente, faz sentido colocar esses itens perto da frente do depósito. Enquanto isso, itens de movimento lento demoram mais para serem revertidos - semanas ou meses em vez de dias. Pode fazer sentido colocá-los na parte de trás do armazém, a menos que sejam relativamente pesados, o que significa que eles podem ser os primeiros na ordem de separação e formar a base do palete.
Zona ou tecnologia
Os armazéns organizados por zona não têm locais de armazenamento permanentes. Em vez de, latas cheias de itens perecíveis vão para zonas refrigeradas, latas cheias de bonecos de ação vão para a zona dos "brinquedos de plástico", itens valiosos vão para uma zona bloqueada e muito mais. Ao alocar itens dentro dessas zonas, deve-se ter cuidado ao colocá-los para facilitar o acesso. Isso significa considerar a tecnologia usada para acessar esses itens - manualmente, escada, empilhadeira e muito mais.
Feedback do selecionador
Os gerentes devem ouvir seus funcionários. Os indivíduos no local de coleta de estoque sabem mais do que os dados podem dizer, e suas sugestões ajudam a otimizar o ambiente de warehouse e melhorar a segurança.
Sazonalidade
A velocidade muda com o tempo. Um item que vende rapidamente durante o verão pode mover-se lentamente durante o inverno. Compreender as informações de velocidade permite que as empresas recolham o armazém e atinjam a eficiência máxima durante todo o ano.
Afinidade do produto
A afinidade do produto é essencial porque esses objetos costumam ser enviados juntos - impressoras e cartuchos de tinta, por exemplo, ou enfeites de Natal e papel de embrulho. Os itens geralmente enviados juntos devem ser posicionados próximos um do outro, quando possível.
Requisitos especiais de armazenamento
Alguns itens - consoles de videogame, smartphones, joias e muito mais - representam um alvo tentador para roubo. Esses itens devem ser agrupados em uma zona enjaulada e observar quem entra e sai. Alimentos perecíveis devem estar em zonas perecíveis, e itens potencialmente tóxicos devem ser armazenados separadamente. Os gerentes devem certificar-se de informar todos os selecionadores sobre os procedimentos de manuseio seguro para itens perigosos ou sensíveis à temperatura.
Algoritmos de alocação de armazém
Os administradores devem considerar vários fatores, e porque há muitos itens sob gestão, é um desafio gerenciar a mudança de prioridades. Muitos gerentes de instalações estão agora recorrendo ao software para orientação.
Um algoritmo de alocação (direto) é o método “ABC”. Este método depende exclusivamente dos dados do histórico de pedidos para medir a velocidade do item. Geralmente, ele coleta os SKUs de todos os itens pedidos nos últimos 30 dias. Esses itens são então agrupados - 50% dos itens com a maioria dos pedidos de linha vão para o grupo A, os próximos 25% como grupo B e os últimos 25% no grupo C. Os itens do grupo A vão mais perto da porta.
À medida que os armazéns lidam com contagens mais altas de SKU e maiores giros de estoque, o método ABC usa sua utilidade. A velocidade não é a única consideração que garante a priorização de um item em detrimento de outro.
À medida que os gerentes das instalações lidam com a complexidade crescente, o software é a melhor e única escolha para alocação de depósitos. Os gerentes de instalações podem definir as medidas de suas caixas de armazenamento, criar sequências de armazenamento / seleção definidas pelo usuário, e combinar essas informações com previsões de demanda para otimizar o warehouse programaticamente. Isso significa que os gerentes de warehouse podem descarregar a responsabilidade de alocação de warehouse e se concentrar em suas competências essenciais.
6 dicas de otimização de alocação de armazém
A alocação de armazém pode funcionar bem, mas não funciona bem por conta própria. O ambiente de warehouse deve estar em conformidade com padrões específicos para ajudar o processo de alocação a atingir seu potencial máximo.
1. Mantenha o armazém limpo e organizado
Slotting envolve organização no nível do slot, mas há mais do que isso. Garantir que as caixas tenham rótulos, os itens se empilham bem e não há material de embalagem descartado obstruindo os corredores, o que significa que o entalhe funciona muito melhor.
2. Avalie a capacidade de armazenamento
A alocação de armazém não funcionará bem, a menos que os gerentes considerem a alocação de macro junto com o micro. Isso significa que a organização do warehouse deve aproveitar o espaço disponível. Isso garante que o processo de alocação nunca seja prejudicado por considerações como excesso ou falta de estoque.
3. Reorganizar o estoque
Lembrar, a velocidade não é o único objetivo final do processo de alocação. Não deve ser apenas fácil chegar a uma prateleira específica - também deve ser fácil encontrar um item nessa prateleira. Isso significa que fatores como rotulagem e organização também precisam ser considerados.
4. Classifique os slots por prioridade
Alguns slots de warehouse são mais críticos do que outros; por exemplo, os slots mais próximos da doca de carregamento são geralmente mais críticos do que os slots na parte traseira. Os slots mais importantes precisam ser preenchidos primeiro.
5. Segurança em primeiro lugar
Em uma linha semelhante, os gerentes nunca devem trocar velocidade por segurança. Esforce-se para manter os funcionários fora do caminho das empilhadeiras, certifique-se de que os materiais do slot resistam ao uso pesado repetido e confirme se os funcionários têm o treinamento para lidar com itens pesados e (ou) perigosos.
6. Investir em um sistema de gerenciamento de armazém
Os sistemas de gerenciamento de depósito (WMS) atuam como uma assistência incrível para os gerentes de instalações que desejam agilizar o processo de otimização do depósito. Ao incorporar dados de todo o warehouse, incluindo histórico de pedidos, SKUs e nível de separação, um WMS pode gerar insights que os humanos sozinhos não alcançariam.
Quando está reelotando uma consideração
A alocação de depósitos não é um processo único. Conforme a demanda do cliente muda, o interior do armazém deve mudar. Quando você reslot?
- Mudanças na demanda:
A sazonalidade pode fazer com que a velocidade do produto mude, Mas isso não é tudo. Uma empresa pode decidir colocar um item à venda, causando um pico de demanda. Os gerentes de instalações devem se coordenar com os profissionais de marketing para antecipar essas mudanças. - Mudanças no mix de produtos:
Novos SKUs estão continuamente entrando e saindo do ciclo de vida do produto. Conforme novos produtos entram ou saem do mercado, os gerentes das instalações precisam continuamente reequilibrar o depósito para dar conta disso. - Choques na cadeia de suprimentos:
Preocupações econômicas mais amplas podem ser sentidas no depósito. A escassez de peças que antes eram amplamente disponíveis pode significar que as empresas não devem enfatizar os produtos anteriormente solicitados.
Eventos desestabilizadores regularmente forçam os gerentes das instalações a reassentar o armazém - mas no verso, um evento desestabilizador é uma oportunidade para otimizar ainda mais o warehouse. Uma vez que as empresas tenham se redefinido para uma arte, eles podem melhorar continuamente as métricas, como selecionar e reabastecer a mão de obra.
Implementar alocação de armazém com NetSuite
A alocação de depósitos é um dos processos de otimização mais críticos que os gerentes de logística devem realizar regularmente. O processo de alocação pode ter uma influência descomunal em uma organização, já que o estado dos itens recebidos influencia a satisfação do cliente. Ninguém quer abrir uma caixa de produtos danificados.
Com um sistema de gerenciamento de armazém da NetSuite, os gerentes de instalações podem eliminar a dificuldade de alocação de depósitos e aproveitar os benefícios. Com recursos como painéis de atividades e rastreamento de vida útil, os gerentes de warehouse agora podem rastrear métricas críticas imediatamente. Esses recursos e benefícios fornecem a eles a visão de que precisam para otimizar o warehouse e reslot conforme necessário.
Com a urgência e a complexidade da logística aumentando, os gerentes das instalações precisam de ferramentas melhores para acompanhar o ritmo. Faça um tour pelo produto hoje e saiba como o NetSuite pode ajudar a transformar o gerenciamento de instalações em um processo de melhoria contínua.
Gestão de stocks
- Quais itens são isentos de impostos sobre vendas na Flórida?
- 5 dicas de dinheiro para melhorar sua economia
- Gerenciamento de estoque de varejo:o que é,
- O que é o Wave Picking? Como funciona,
- 5 dicas para economizar para a faculdade e aposentadoria
- O que é Literacia Financeira e como melhorá-la
- 51 dicas de gerenciamento de armazém para o seu negócio
- 8 dicas rápidas para uma busca de emprego bem-sucedida
-
Use estas dicas para melhorar seu crédito
Goste você ou não, o crédito é parte integrante da economia moderna, mercado imobiliário, e status quo bancário. Se você tem crédito ruim, você sentirá isso em sua vida financeira. Você não poderá faz...
-
O que é produtividade? Um guia comprovado para melhorar sua produtividade
Bem-vindo a este guia de produtividade. O objetivo deste guia é duplo. Primeiro, Vou definir o que é produtividade. Muitas vezes, tentamos melhorar a produtividade sem saber o que é. Segundo, Eu compa...